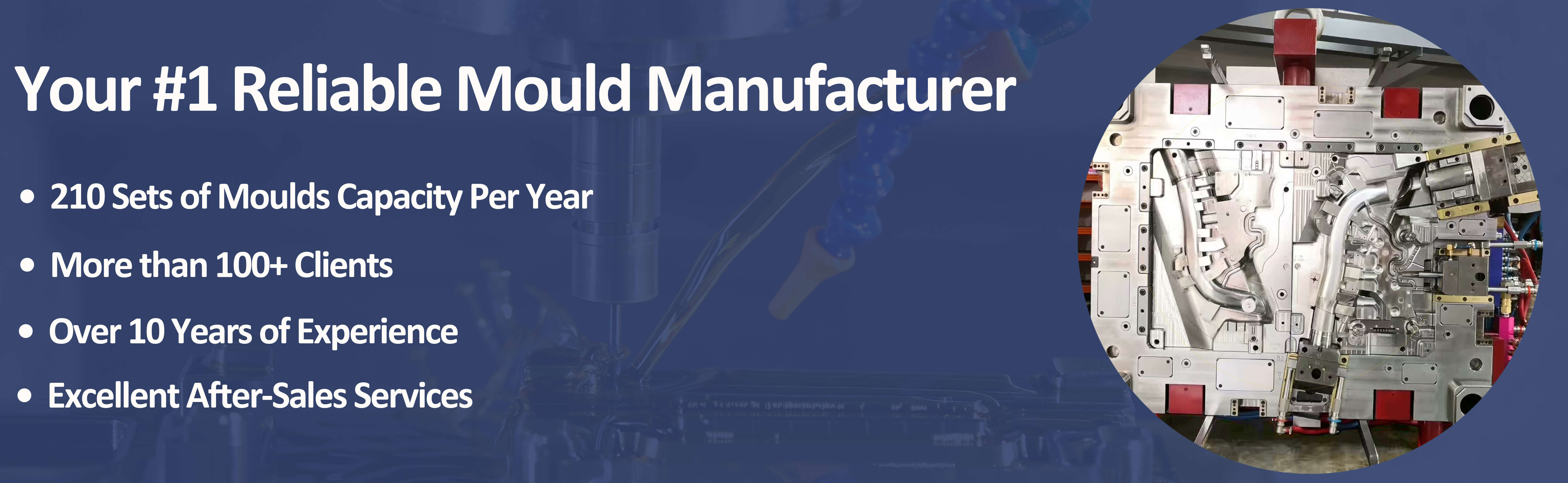
![]() |
|
Advantage of Mould Manufacturing
✔ Outstanding Engineering Team for Export Molds
✔ Rich Experience Manufacturing Team
✔ Up to Date Equipment
✔ Quality Guarantee with ISO 9001:2015
✔ Fast Delivery Time
✔ Excellent After-sales service
|
![]() |
![]() |
![]() |
MOLD-MAKING FACTORY |
WIRE CUTTING |
EDM |
![]() |
![]() |
![]() |
CNC AREA |
CNC+EDM LINE |
IMM-MOLD TRIAL |
Injection Mould Manufacturing With intense mould design experiences and excellent craftsmanship, Lyter produces more than 300 molds for customers from Germany, USA, UK, France, Spain, Slovenia, Canada, and other countries as a reliable Chinese Injection Mould vendor.
Among different tooling manufacturers, for molds made by Lyter will have below advantages: - Outstanding design and engineering team to take over the project from the very beginning.
- Manufacturing team with excellent craftsmanship to make every inserts and have them well fitted, and to make sure the mold is easy for maintenance and best durability.
- Moulding team with rich experiences will have the mould trial optimized to best-in-class cycle time.
- All design, fabrications and moulding activities are under control by quality guarantee with ISO 9001:2015. |
|
![]() |
![]() |
|
|
![]() |
|
Lyter’s General Steel Selection for Precision Mould Making
American Standard #: AISI 1050 ~ 1055; Japanese Standard #: S50C ~ S55C German Standard #: 1.1730. 2. 40 Cr Mn Mo 7 (Pre-hardened steel) For USA, Japan, Singapore, Hong Kong SAR and China, the code is AISI P20, for Germany and some European countries the code is DIN: 1.2311, 1.2378 & 1.2312. 3. X 40 Cr Mo V51 (Hot work Steel) For USA, China, Hong Kong SAR & Singapore, the code is AISI H13; for Europe it is DIN 1.2344, for Japan it is SKD61. 4. X45 Ni Cr Mo 4 (Cold work steel) The standard code for USA, China, Hong Kong SAR & Singapore is AISI 6F7, for Europe it is DIN 1.2767. 5. X42 Cr 13 (Stainless steel) The standard code for USA, China, Hong Kong SAR & Singapore is AISI 420 STAVAX, for Europe it is DIN 1.2083. 6. X 36 Cr Mo 17 (Pre-hardened stainless steel) The standard code and European code are AISI 420 STAVAX and DIN 1.2316 respectively. 7. X 38 Cr Mo 51 (Hot work steel) The standard code and European codes are AISI H11 and DIN 1.2343 respectively. 8. S 7 heavy-duty tool steel This steel is usually used by American customers. 9. X 155 Crvmo 121 Cold Work Steel The standard code is AISI D2. And the European code is DIN 1.2379, while for Japanese it is JIS SKD11. 10. 100 Mn Cr W4 & 90 Mn Cr V 8 (Oil steel) They are AISI 01 & AISI 02 for the standard code, and DIN 1.2510 & DIN 1.2842 for the European code. 11. BeCu This material is used in places where it is difficult for cooling in plastic molds, as BeCu copper has much better thermal conduction than that of general steels. |
|
APPLIANCE
ENERGY
AUTOMOTIVE
MEDICAL
ELECTRONICS
INDUSTRIAL
AVATION
Who is your main steel supplier?
LYTER---This depends on customer requirements, for imported steel, we usually use SCHMOLZ+BICKENBACH and GROEDITZ and FLNK. For domestic steel, we always use the best supplier in china, like LKM、FUSHUN.
Who make the polishing? In house or out house?
We have polishing workers in house. But for really higher polishing requirement, for examples, A1 stand polishing, we outsource, The supplier is about 3km away from our company.
LKM and Ftaba for standard mold base of our plastic injection mold.
If the mold base is non-standard, we will use suppliers which we have cooperated for a long time and their quality is proved very good.
It depends on customer requirements. We mainly use hot runner suppliers like HRS, Yudo, Incoe, Moldmasters, Synventive etc.
There are various types of molds for mold manufacturing. And the most common types are 2 plate mold, 3 plate mold/pin-point gate mold, hot runner manifold mold, thoroughly harden mold, and pre-hardened mold.
1)The two-platen mold, also known as the single parting surface mold, is the simplest type of injection mold. It divides the entire mold into two parts based on the parting surface: Moving mold and fixed mold. Part of the cavity is in the moving mold; part of the cavity is in the fixed mold. The main runner is in the fixed mold; the runner is located on the parting surface. After the mold is opened, the product and the runner remain in the moving mold, and the moving mold Some have an ejection system. Here is an image for your reference.
2)There are two parting surfaces that divide the mold into three parts, and a gate plate is added to the two-plate mold. This kind of mold uses a pointed gate, so it is called a pin-point gate mold.
3)With the help of a heating device, the plastic in the injection system will not solidify and will not be demolded with the product, so it is also called a non-runner mold.
4)The steel used in the inner mold part needs to be heat treated (such as quenching) after being purchased to meet the requirements of use, such an injection mold is called a hard mold.
5)The steel used in the inner mold part does not need to be heat-treated after purchasing, and it can meet the requirements of use. Such an injection mold is called a soft mold.
With the development of computer technology, CAD technology has become an important tool for product designers to conduct research and development. Among them, three-dimensional modeling technology has been widely used in product and mold design, program review, automated manufacturing, as well as management and maintenance. In the actual development and manufacturing process, the technical data received by designers may be three-dimensional models of various data types, but in many cases, they are physical models of products obtained from upstream manufacturers. Designers need to use a certain way to convert this physical information into CAD models, which is applied to reverse engineering technology.
There are several characteristics of mold manufacturing. Here are some of them for your information.
1.Mold manufacturing belongs to single-piece, multi-variety production. Each mold can only produce a single product, and the mold is generally not universal.
2.Customers require a short mold manufacturing cycle.
3.Complete set of mold manufacturing.
4.The precision of the mold is high, and the precision depends on the precision of the machine tool, processing technology, and measurement methods.
5.In the mold manufacturing process arrangement, the process is relatively concentrated to ensure the quality and progress of mold processing, simplify management, and reduce process turnaround time.
6.Mold working parts have complex shapes, high material hardness, heat treatment needs to be arranged in the mold manufacturing process.
The basic requirement of mold manufacturing is to shorten the molding cycle and reduce mold costs as much as possible on the premise that the accuracy and life of the mold meet customer requirements.
The technical and economic indicators of the mold include mold accuracy, mold production cycle, mold production cost, and mold life. In the mold manufacturing process, the following four technical and economic indicators should be considered comprehensively
The four technical and economic indicators of the mold influence and restrict each other, and must be considered comprehensively to obtain the best economic benefits and meet production needs.
What is the common heat treatment technology for Mold Manufacturing?
According to the working conditions of the mold manufacturing, the mold can be divided into two types: cold work mold and hot work mold, and the heat treatment process is slightly different.
1.Cold work dies: It requires high hardness, high wear resistance, and certain toughness, so this type of die steel often contains high carbon content. Therefore, pre-heat treatment after forging and final heat treatment after machining is required. The usual heat treatment process is Spheroidizing annealing, quenching + low-temperature tempering, sometimes chemical heat treatment is required, such as carburizing, nitriding, carbonitriding, etc., surface quenching, stress relief annealing, and individual precision molds also need to be stabilized tempering or supplementary tempering.
2. Hot working die: Since the processing object is often the steel heated to the austenitic state, it needs a certain degree of hardness and high wear resistance. Due to forging, it needs high impact toughness. Therefore, this type of steel is often medium for carbon steel and medium carbon alloy steel, the heat treatment process commonly used is quenching and tempering process or quenching + high-temperature tempering, and sometimes spheroidizing annealing is also required.
© Copyright: 2025 Lyter Engineering Ltd. All Rights Reserved
IPv6 network supported